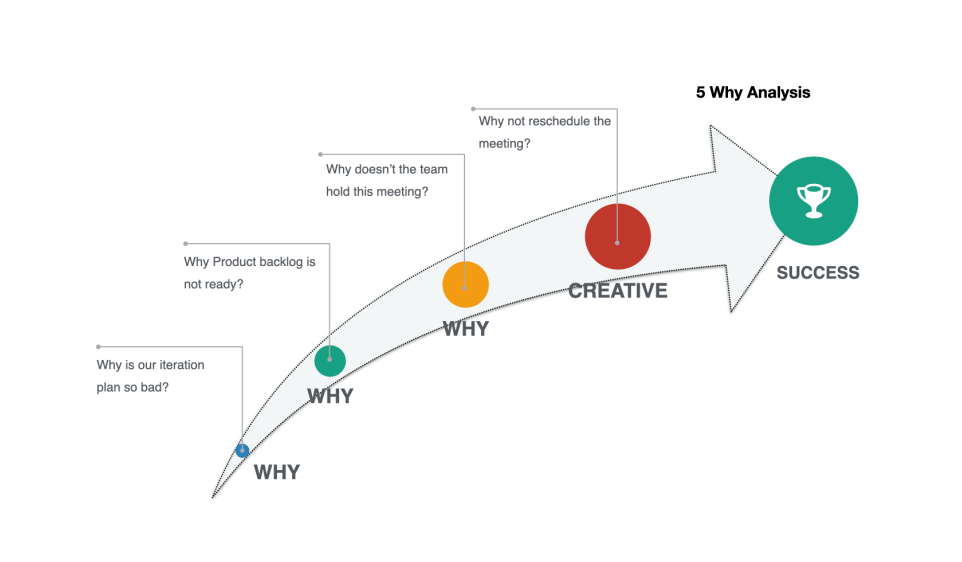
The “Five Whys” technology was proposed in the 1930s by Sakichi Toyoda, Later Toyota Motor Corporation adopted this method in the process of improving its manufacturing methodology. This has become a key content in the induction course of Toyota Production System.
What is the 5-why analysis method?
The 5why analysis, also known as the “why-why” analysis method, also known “five-question method” is a method of using the “why” repeatedly for 5 consecutive times to find the root cause of the problem. This method is suitable for anlyzing simple to complex problems.
Simply ask the question continuously (“5 whys”) till you find the root cause of the problem & loopholes, and then work on the preventive measure to prevent the problem from appearing again. Although this method is called as 5 whys, It is not limited to “5 whys” when used, because the rootcause of the problem can be found by repeatedly asking 5 whys, some time 1 whys, some times it may take 15 whys.
Real time example to understand the 5whys?
Let’s get a preliminary understanding of the “5 whys” analysis method through real-time use case. Let us consider a use case related to a bad iteration plan in the agile process. So how can the 5 why analysis be applied in the agile process, below an example
- Why-01: Why is our iteration plan so bad?
- Ans-01: Because we don’t have a clear goal, and the Product backlog is not ready.
- Why-02: Why Product backlog is not ready?
- Ans-02: Because the team did not hold a product backlog refinement meeting.
- Why-03: Why doesn’t the team hold this meeting?
- Ans-03: Because it was originally planned to have a meeting on Thursday afternoon from 10:00 to 14:00, but the Delivery head happened to talk to the leader of the team at the same time.
- Why-04: Why not reschedule the meeting?
- Ans-04: Because there is no meeting host.
Therefore, the real root cause of the poor iteration plan is the responsibility of the product backlog refinement meeting. In this case, we can find a responsible person from the Scrum team and reach an agreement on the expected timetable for implementing the improvement measures.
Rules to perform why analysis
In order to perform a 5 whys analysis appropriately, the below following rules should be followed
- You need to find the right team to complete this fault reflection.
- Use whiteboard or paper to discuss about the problem.
- Write down the entire process of the problem to make sure everyone can understand it.
- Distinguish the causes and symptoms.
- Pay special attention to causality.
- Explain the Root Cause and related evidence.
- The 5 why answers need to be precise.
- Steps to find the source of the problem instead of jumping directly to the conclusion.
- To be based on objective facts, data and knowledge.
- Evaluation process rather than people.
- Never take “human error” or “blame game” as the source of the problem.
- Cultivate an atmosphere and culture of trust and sincerity.
- Keep asking “why” until the root of the problem is found.
- When you give a “why” answer, you should answer from the user’s perspective.
Conclusion
Repeat five times, and the nature of the problem and its solution are immediately evident. Currently, this method has been widely adopted in Lean Manufacturing, and Six Sigma.